The Engineering behind Plastic Extrusions & Custom Profile Extrusion
Plastic extrusions are the technology to mold raw plastic and produce tubes, channels, pipes, or consumer durables. Many extrusion engineering methods are available to manufacture plastic profile through custom profile extrusion. Plastic extrusions engineering is the answer to any type of prototyping methodology as well.
As the plastic profile and custom profile extrusion market is growing rapidly worldwide, customers now looking for reliable cost-effective sources. One of these sources is China Plastic Extrusion that offers services like readymade plastic profile, and customized extruded channels. The company is also the trusted source of raw plastic for the extrusion process. Clients also contact China Plastic Extrusion for expert consultation on custom profile extrusion.
Defining the Engineering of Plastic Extrusions and Custom Profile Extrusion
Plastic extrusion is the technology used to reshape and resize plastics to manufacture different consumer items. For example, window channels, door channels, weather-stripping materials, toys, amusement park setups, home construction items, etc. are the produce of plastic extrusion.
A. The Process of Plastic Extrusions
Plastic is extruded by liquefaction of polymeric beads, passed through a mold cast opening, at the front side of the extruder machine, through melt and transfer screw transportation process.
The method of custom profile extrusion or plastic profile manufacturing can have five sections as follows:
1. Feeding of Raw Plastic and Additives to the Extruding Machine
- The method begins by adding a definite raw material of polymeric compound, as required by the product specifications.
- The raw material goes into a hopper fitted above the screw entry mouth at the backside of the extruder machine.
- Several additives are also included in the hopper. These are colorant, UV-resistant chemicals, etc.
2. The Process of Melt and Transfer Screw Conveyance
- The screw, and barrel-shaped apparatus that contains the screw, are heated through coils, and as a result, melts the polymer raw material.
- The melting process is a stepped staging process.
- As the screw rotates the molten raw material proceeds toward the front end of the extruder machine.
- In a certain process, there could be a set of sieving screens in the path of the molten plastic fluid. These screens remove any debris, silt, contaminants that could be there in the liquid plastic.
- Other manufacturing experts say that the inclusion of the sieving screen increases the uniformity of the molten liquid. This in turn increases the tensile strength of the finished product.
3. Forcing Molten Plastic into the Custom Die or Casts
- At the front end of the extruder machine, the molten polymer is passed through an opening in the shape of the product that is designated to be manufactured.
- The die or cast could be a channel shape, profile shape, a rod, a tube, or any possible geometrical shape.
- Once the semi-liquid plastic profile exits the front of the machine, the melted structure is guided into a tool intended to set the material up into the size and shape of the finished item.
- A sizing tool then forms this finished item into the shape and size necessary by the product specifications.
4. Downstream Process to Extract the Extruded Products
- As the plastics extrusions method is a fluid melt process, the shape and size of the material being extruded are governed by an extruder operator and specialist tooling apparatus.
- The extruder operator must supervise the control parameters and barrel heating temperature.
- A skilled operator needs to control conditions for both the melting of plastic, as well as the cooling of the profile in the downstream phases of the manufacturing operations.
- A takeoff machine unit is set up at the end of each plastic extrusion production line.
- The takeoff pulls the custom profile extrusion material as it exits the extruder machine, and basically is what governs the production line speed.
- Also, to some extent, the takeoff unit controls the plastic material size, as it pulls tension on the finished product and preserves stability throughout the course of the manufacturing.
5. Collection, Packaging, and Transportation of Finished Plastic Profile
- These custom profile extrusion products are then cut into specific lengths as per consumer requirements.
- Certain plastic extrusions products are also coiled or winded in spools.
- The packaging depends on the finished plastic profile, either it is flexible or rigid.
- After cutting or spooling, custom profile extrusion products are then packaged into an appropriate packaging vessel as specified by the client.
- Packaging materials include bundles, boxes, or bulk put-ups, which are then transported to the market or client warehouse.
B. Types of Plastic Profile Being Manufactured
China Plastic Extrusion is producing every kind of readymade plastic extrusion items or custom profile extrusion products as required by the consumer. The company can virtually give any channel or profile shape to plastics through its state-of-the-art production line. Some of the widely sold products are as follows:
1. Polypropylene or Polyethylene
- Economical resins that are lightweight available in standard and particular grades.
- Both solid and hollow profiles are designed and produced as per client configurations.
- Competency in manufacturing custom cut length plastic profile.
- Ability to produce plastic extrusions in custom or standard colors.
2. Nylon Polyamide 6 & 12
- Better heat-resistant custom profile extrusion products.
- Great wear-resistant plastic profile materials.
- Plastic extrusions producing materials resistant to chemicals and oils.
- Profiles are available in rigid and flexible grades.
- Excellent rigidity and strength throughout the manufacturing batches.
3. Acrylic Profiles or Polycarbonate (PC)
- Acrylic profiles offer precision fabrication and tolerance cutting.
- Huge collection of most widely used colors with color matching proficiencies.
- Time-saving production and finished goods shipping.
- Crystal clear plastic beads, powder, or resins stock available in grades including UV, FDA, FR, and general-purpose.
- Polycarbonate (PC) custom profile extrusion products also support hollow or solid plastic channels, rods, or strips.
China Plastic Extrusion can extrude almost all thermoplastic materials into profile shapes through custom profile extrusion. Also, the company offers production of an ‘as specified’ basis by evolving tooling and product to the client’s configuration.
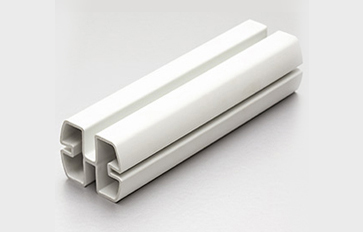
China Plastic Extrusion also offers angle-cutting, specialty-cut lengths, custom color, post-extrusion fabrication, and tape application as part of the custom profile manufacturing contract. Approximately half of our production output is custom-extruded plastic items. Hence, the company has significant confidence in the capability to manufacture your profile to exact specifications.
Uses of Plastic Profile Manufactured Through Plastic Extrusions
Plastic extrusions engineering finds many uses in day to day life and some of them are:
1. Custom Profile Extrusion That Produces Amusement Park Materials
It is the biggest market for plastic extruded items like toys, rides, sitting arrangements, landscaping, rails for toy trains, barricading grills, etc.
The use of plastic to make toys for children is safer in comparison to metal or wooden toys.
2. Food Industry Example for Plastic Extrusions
The food industry requires specially extruded plastic frames, tubes, or pipes. These are made through custom profile extrusion.
3. Shoe Molding
In recent days, the usage of items made from plastic extrusions can be seen in baseboard molding of house flooring.
4. Plastic Extrusions in Landscaping Industry
Custom profile extrusion molding can be used in a manner that can fit height or width as required to secure rocks, soil, or plant beds.
Concluding Words
Plastic is the most affordable raw material used for the manufacturing of many consumer durables. Plastic is also resistant to wear and tear. As a result, it lasts longer than wood or metal. However, it is a challenge to give plastic a desired shape, and rigidity that it needs to be durable. This hurdle is overcome by plastic extrusions. China Plastic Extrusion is the trusted name when you need custom profile extrusion to produce a plastic profile.